当3D打印关节技术在医疗行业得到普遍应用之后,那些过去只能在科幻电影里看到的场景,如今已在现实中逐步实现。近日,一家生物医药公司安聚德完成了其利用纳米生物陶瓷等新材料3D打印机制人体骨骼的流水线安装、调试,而研发设计出这样一条全新生产线的是来自航天基地的宝科流体公司。
将企业比拟为“设计院”的宝科董事长张旭介绍说,当前,随着“中国制造2025”的快速推进,工业制造以机器人替代人工成为必然趋势,然而采用传统工业机器自动生产线难以满足现代多品种、小批量、供货紧的柔性智能制造需求;特别是 “大数据”给产业插上了腾飞的翅膀,定制化生产、服务将成为企业推动制造装备升级、增强生产竞争能力的一个新增长点。
可是在很多行业中,企业的柔性生产之路因为专项人才匮乏、企业主知识面局限、重金购买的设备不能完全匹配实际生产要等各式各样的现实原因,并没那么好走。比如西北地区很多的原料药制药厂家,到现在还要靠人工手动去为生产不一样的药品配比原料。
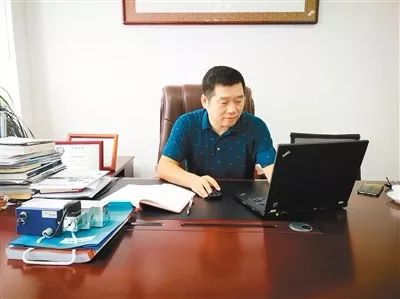
“而我们擅长的就是为各类企业量身定制,研发出适应多品种、快速定制化产品的生产线,让机器们‘乖乖听话’,整个环节在节省人力成本的同时流畅自如,提升产品制造效率。”张旭表示,经过多年的发展,目前企业已经开发出了包括航空航天、精细化工、生物制药、餐饮、冶金等行业的多种设备或系统,部分设备系统在行业或领域占有率超过1/3。
同时,企业还参与到为我国自主研制的C919大型客机研发飞机机舱疲劳、静力试验台,为总参工程兵科研三所提供模拟隧道施工中安全防范技术方案等难点重重的工业领域设计研发中,为在工业制造专业领域打破国外垄断、赶超世界先进而不懈努力。
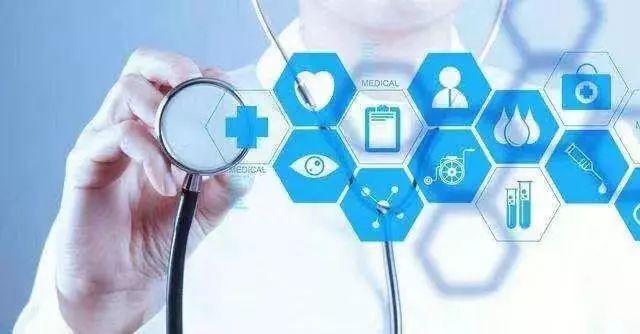
在长期为国内钢厂供应进口装备期间,他发现国内的冶炼企业很难脱除炉内的碳、氢等杂质,合金比例也难均匀,“这也是我国难以生产出高品质钢材和有色金属的原因之一。”因此,张旭和团队就以冶金领域为突破口,首创开发出冶金行业智能底吹系统,很好地解决了冶金领域中金属液体内去除杂质和快速均匀成分的技术难题。
“以前,因为技术不过关,我国只能将粗钢卖给国外,再高价购买国外的‘细钢’、‘特钢’用于汽车、飞机制造等。”随着宝科顺利攻破这一技术难题,不但进一步提升了以洁净钢平台建设为重点的工艺技术,而且也引领了国内以及国际此技术的发展。据介绍,目前这一系统已在国内200多家大型钢厂大范围的应用,并长期给国内20余家电炉研究院所配套使用,产品先后出口到土耳其、印度、孟加拉、越南、泰国等。
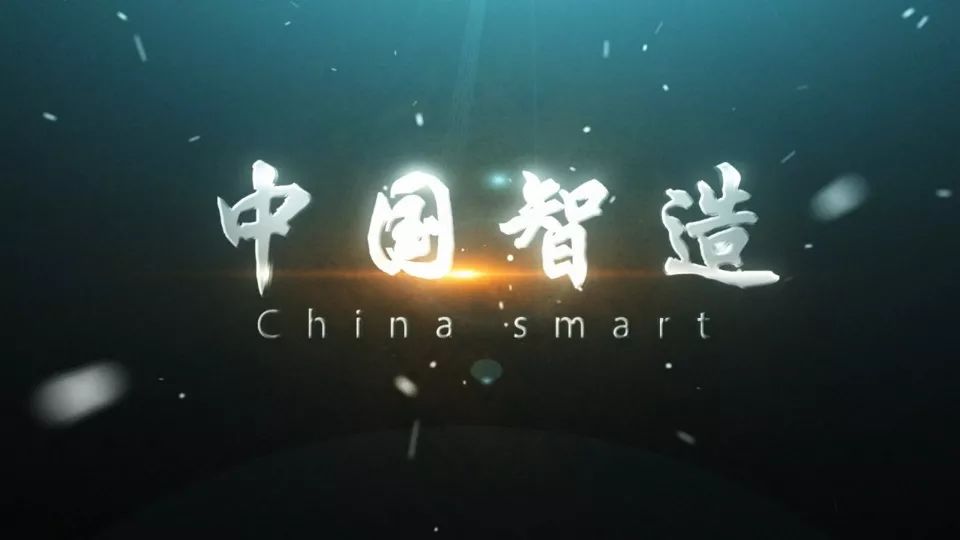
此外,宝科团队还与德国西门子合作,设计研发宝科MES控制系统软件。据了解,MES即制造公司制作过程执行系统,是一套面向制造企业车间执行层的生产信息化管理系统。MES可以为公司可以提供包括制造数据管理、计划排产管理、生产调度管理、人力资源管理、成本管理、底层数据集成分析、上层数据集成分解等管理模块,为企业打造一个扎实、可靠、全面、可行的制造协同管理平台。
“目前国内某年产100吨的石墨烯生产系统、国内某银粉制取生产系统、锂离子阳极材料生产线等,都是由我们为企业方设计MES系统,从而完成产线优化,提高产能的。”宝科团队年轻的销售经理姜健介绍说。
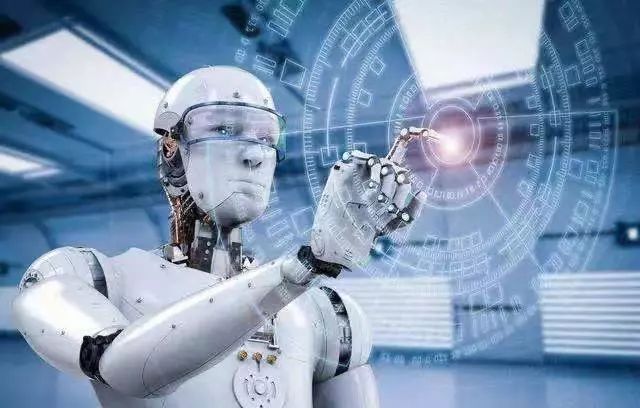
“高端装备制造业是以高新技术为引领,处于价值链高端和产业链核心环节,决定着整个产业链综合竞争力的战略性新兴起的产业,是现代产业体系的脊梁,是推动我们国家工业转型升级的引擎。”
张旭说,随着“中国制造2025”的展开,众多行业领域都很大程度涉及人机一体化智能系统,作为西安民企能够带领团队抓住机遇、去参加了,逐步的提升工业互联技术,提高智能传感技术、模块化工艺制造控制技术、数据通讯传输及终端显示技术在研发生产线中的应用,普及、助力我国装备制造向高端、智能、精益的转变,感觉很幸运、很值得、很骄傲。